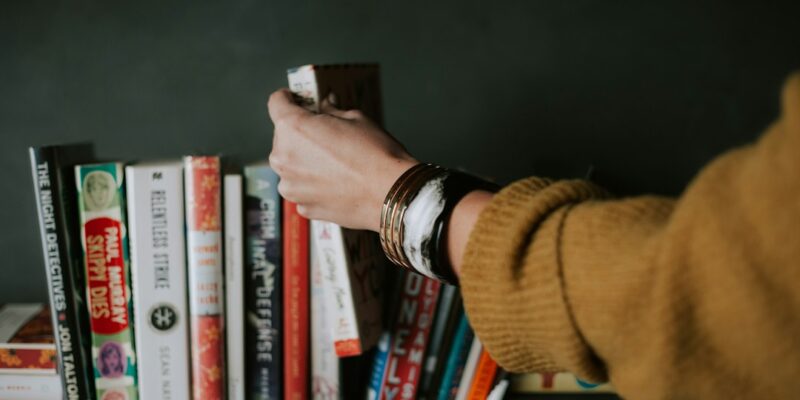
Exploring the Fascinating World of Non-Destructive Testing: A Must-Read Book for Engineers and Technicians
Non-Destructive Testing (NDT) is a method used to evaluate the integrity and quality of materials and components without causing any damage or destruction. It is an essential process in various industries, including manufacturing, aerospace, oil and gas, automotive, and construction. NDT plays a crucial role in ensuring the safety, reliability, and efficiency of products and structures.
In this blog post, we will explore the history and evolution of NDT, the different methods and techniques used in NDT, the role of NDT in various industries, such as aerospace, oil and gas, automotive, and construction, and the future of NDT with advancements in technology. We will also discuss the importance of training and certification for NDT professionals.
Key Takeaways
- Non-Destructive Testing (NDT) is a crucial process used to evaluate the integrity of materials and components without causing damage.
- NDT has a long history, dating back to ancient times, and has evolved to include modern techniques such as ultrasound and digital radiography.
- There are various methods of NDT, each with its own advantages and disadvantages, including visual inspection, magnetic particle testing, and eddy current testing.
- NDT plays a vital role in improving quality and safety in industrial applications, including aerospace, oil and gas, automotive, and construction industries.
- The future of NDT looks promising with advancements in technology and emerging applications, but it is important for NDT professionals to receive proper training and certification to ensure competence and compliance.
The History and Evolution of NDT: From Ancient Times to Modern Applications
The concept of non-destructive testing can be traced back to ancient times when craftsmen used visual inspection to assess the quality of their work. However, it was not until the 19th century that more systematic methods of NDT began to emerge.
One of the earliest methods of NDT was radiography, which was developed in the late 19th century. This technique uses X-rays or gamma rays to penetrate materials and create images that can reveal internal defects or structures. Radiography revolutionized NDT by allowing inspectors to see inside objects without causing any damage.
In the 20th century, advancements in technology led to the development of other modern NDT techniques. Ultrasonic testing became widely used during World War II for inspecting welds on ships. This technique uses high-frequency sound waves to detect flaws or measure material thickness. Magnetic particle testing and liquid penetrant testing were also developed during this time, providing inspectors with additional tools for detecting surface cracks or defects.
Advancements in technology, such as the use of computers and digital imaging, have further enhanced the capabilities of NDT. Digital radiography and computed tomography (CT) scanning have become more common, allowing for more detailed and accurate inspections. The use of robotics and automation in NDT has also increased efficiency and reduced human error.
The Different Methods of NDT: Understanding the Pros and Cons of Each Technique
There are several different methods and techniques used in non-destructive testing, each with its own advantages and limitations. Here are some of the most commonly used techniques:
1. Visual inspection: This is the simplest and most basic form of NDT, involving a visual examination of the surface or structure being inspected. It is often used as a preliminary method to identify any obvious defects or abnormalities. Visual inspection is non-intrusive and relatively inexpensive, but it may not be able to detect internal defects or flaws.
2. Radiography: This technique uses X-rays or gamma rays to create images of the internal structure of an object. It is particularly useful for detecting internal defects, such as cracks or voids, in materials like metal or concrete. Radiography provides detailed images that can be analyzed by trained inspectors, but it requires specialized equipment and trained personnel to operate safely.
3. Ultrasonic testing: Ultrasonic testing uses high-frequency sound waves to detect flaws or measure material thickness. It is commonly used for inspecting welds, pipes, and other structures made of metal or composite materials. Ultrasonic testing can provide accurate measurements and detect both surface and subsurface defects, but it requires skilled operators and can be time-consuming.
4. Magnetic particle testing: This technique is used to detect surface cracks or defects in ferromagnetic materials, such as iron or steel. It involves applying a magnetic field to the material and then applying iron particles to the surface. If there is a defect, the particles will be attracted to it, making it visible to the inspector. Magnetic particle testing is relatively quick and inexpensive, but it can only detect surface defects and requires direct access to the material being inspected.
5. Eddy current testing: Eddy current testing is used to detect surface or near-surface defects in conductive materials, such as metal. It works by inducing an electrical current in the material and then measuring changes in the current caused by defects. Eddy current testing is fast and can be used on a wide range of materials, but it is limited to detecting surface or near-surface defects.
6. Liquid penetrant testing: This technique is used to detect surface defects, such as cracks or porosity, in non-porous materials. It involves applying a liquid dye to the surface of the material, allowing it to penetrate any defects, and then removing the excess dye. The remaining dye is then made visible using a developer. Liquid penetrant testing is relatively simple and inexpensive, but it can only detect surface defects and requires direct access to the material being inspected.
Each NDT technique has its own advantages and limitations, and the choice of method will depend on factors such as the type of material being inspected, the type of defect being sought, and the available resources and expertise.
The Role of NDT in Industrial Applications: How it Improves Quality and Safety
NDT Method | Application | Benefits |
---|---|---|
Ultrasonic Testing | Weld inspection | Detects internal defects, ensures weld integrity |
Magnetic Particle Testing | Surface crack detection | Identifies surface cracks, prevents catastrophic failures |
Visual Inspection | General inspection | Identifies surface defects, ensures product quality |
Eddy Current Testing | Material sorting | Distinguishes between different materials, ensures correct usage |
Radiographic Testing | Internal inspection | Detects internal defects, ensures product quality and safety |
Non-destructive testing plays a critical role in various industries by ensuring the quality, safety, and reliability of products and structures. Here are some of the key reasons why NDT is important in industrial applications:
1. Importance of NDT in manufacturing: In the manufacturing industry, NDT is used to inspect raw materials, components, and finished products to ensure they meet quality standards. By detecting defects or flaws early in the production process, manufacturers can prevent costly rework or product failures. NDT also helps manufacturers comply with industry regulations and standards.
2. Benefits of NDT in ensuring quality and safety: NDT techniques can detect defects or flaws that may not be visible to the naked eye, allowing for early detection and prevention of potential failures. This helps ensure the quality and reliability of products and structures, reducing the risk of accidents, injuries, or damage. NDT also helps identify areas of weakness or degradation in materials or structures, allowing for timely repairs or replacements.
3. Examples of NDT in industrial applications: NDT is used in a wide range of industrial applications, including the inspection of welds, pipes, pressure vessels, turbines, bridges, and buildings. In the automotive industry, NDT is used to inspect critical components such as engine blocks, suspension systems, and safety systems. In the oil and gas industry, NDT is used to inspect pipelines, storage tanks, and offshore structures. In the aerospace industry, NDT is used to inspect aircraft components such as wings, fuselages, and engines.
NDT in Aerospace and Aviation: Ensuring the Integrity of Critical Components
Non-destructive testing plays a crucial role in the aerospace and aviation industry by ensuring the integrity and safety of critical components. The aerospace industry has some of the most stringent quality and safety requirements, and NDT is an essential part of the manufacturing and maintenance processes.
The use of NDT in aerospace and aviation is particularly important because any failure or defect in an aircraft component can have catastrophic consequences. For example, a crack in an aircraft wing could lead to a structural failure during flight. By using NDT techniques such as radiography, ultrasonic testing, and eddy current testing, inspectors can detect internal defects or flaws that may not be visible to the naked eye.
NDT is used throughout the lifecycle of an aircraft component, from manufacturing to maintenance and repair. During manufacturing, NDT is used to inspect welds, composite materials, and other critical components to ensure they meet quality standards. During maintenance and repair, NDT is used to inspect aircraft structures, engines, and other components for signs of wear, corrosion, or damage.
The use of NDT in the aerospace industry has significantly improved safety and reliability. By detecting defects or flaws early in the manufacturing process or during maintenance inspections, potential failures can be prevented, reducing the risk of accidents or incidents. NDT also helps extend the lifespan of aircraft components by identifying areas of weakness or degradation that may require repairs or replacements.
NDT in the Oil and Gas Industry: Reducing Risks and Ensuring Efficiency
Non-destructive testing is of utmost importance in the oil and gas industry, where the integrity of pipelines, storage tanks, and offshore structures is critical for safety and efficiency. The oil and gas industry operates in harsh environments and deals with highly flammable and hazardous materials, making the need for reliable inspection methods even more crucial.
NDT techniques such as radiography, ultrasonic testing, magnetic particle testing, and liquid penetrant testing are commonly used in the oil and gas industry to inspect pipelines for corrosion, weld defects, or other forms of damage. These techniques allow inspectors to identify potential weaknesses or defects that could lead to leaks or failures.
In addition to ensuring safety, NDT also plays a role in improving efficiency in the oil and gas industry. By detecting defects or flaws early on, operators can plan maintenance activities more effectively, reducing downtime and optimizing production. NDT also helps identify areas of corrosion or degradation that may require targeted interventions to prevent further damage.
The use of NDT in the oil and gas industry has significantly reduced risks associated with pipeline failures or leaks. By implementing regular inspection programs using NDT techniques, operators can identify potential issues before they escalate into major incidents. This not only protects the environment but also helps maintain public trust in the industry.
NDT in the Automotive Industry: Enhancing Quality and Reliability
Non-destructive testing is an essential part of the automotive industry, where the quality and reliability of vehicles are paramount. NDT techniques are used to inspect critical components such as engine blocks, suspension systems, safety systems, and welds.
In the automotive industry, NDT is used during the manufacturing process to ensure that components meet quality standards. For example, ultrasonic testing is commonly used to inspect welds in car bodies to detect any defects or flaws that could compromise structural integrity. Radiography is also used to inspect engine blocks for internal defects or cracks.
NDT is also used during vehicle maintenance and repair to identify potential issues or defects. For example, ultrasonic testing can be used to measure the thickness of brake pads or detect cracks in suspension components. Magnetic particle testing can be used to inspect engine components for surface defects or cracks.
The use of NDT in the automotive industry has improved the quality and reliability of vehicles. By detecting defects or flaws early on, manufacturers can prevent costly recalls or warranty claims. NDT also helps ensure the safety of vehicles by identifying potential issues that could lead to accidents or failures.
NDT in the Construction Industry: Ensuring Structural Integrity and Safety
Non-destructive testing plays a crucial role in the construction industry by ensuring the structural integrity and safety of buildings, bridges, and other structures. NDT techniques are used to inspect materials such as concrete, steel, and composite materials for defects or weaknesses.
In the construction industry, NDT is used during the design and construction phases to ensure that structures meet safety standards and regulations. For example, ultrasonic testing can be used to measure the thickness of concrete walls or detect voids or delaminations. Radiography can be used to inspect welds in steel structures for defects or cracks.
NDT is also used during maintenance and repair activities to assess the condition of existing structures. For example, ground-penetrating radar can be used to detect voids or deterioration in concrete structures. Ultrasonic testing can be used to measure the thickness of steel beams or detect corrosion.
The use of NDT in the construction industry has improved the safety and durability of structures. By detecting defects or weaknesses early on, contractors can take corrective actions to prevent failures or accidents. NDT also helps extend the lifespan of structures by identifying areas of degradation or deterioration that may require repairs or reinforcements.
The Future of NDT: Advancements in Technology and Emerging Applications
The field of non-destructive testing is constantly evolving, driven by advancements in technology and emerging applications. Here are some of the future trends and developments in NDT:
1. Emerging technologies in NDT: New technologies such as 3D scanning, robotics, and artificial intelligence are being integrated into NDT processes, allowing for more accurate and efficient inspections. For example, 3D scanning can create detailed digital models of structures or components, allowing for better analysis and visualization of defects. Robotics can be used to automate inspection processes, reducing human error and increasing productivity.
2. Potential applications of NDT in new industries: As NDT techniques become more advanced and versatile, they are being applied to new industries and sectors. For example, NDT is being used in the renewable energy industry to inspect wind turbine blades for defects or damage. NDT is also being used in the medical field for imaging and diagnostics.
3. Impact of future advancements on NDT: Future advancements in technology are expected to further enhance the capabilities of NDT and improve its efficiency and accuracy. For example, the use of machine learning algorithms and artificial intelligence can help automate defect detection and analysis, reducing the need for human intervention. The development of new sensors and imaging techniques can also provide more detailed and accurate inspections.
The Importance of Training and Certification for NDT Professionals: Ensuring Competence and Compliance
Proper training and certification are essential for NDT professionals to ensure their competence and compliance with industry standards. NDT techniques require specialized knowledge and skills, and it is important for professionals to undergo formal training and certification programs.
Certification programs for NDT professionals are offered by various organizations, such as the American Society for Nondestructive Testing (ASNT) and the International Organization for Standardization (ISO). These programs typically involve a combination of classroom training, practical experience, and examinations.
Benefits of hiring certified NDT professionals include:
1. Expertise and competence: Certified NDT professionals have undergone rigorous training and have demonstrated their knowledge and skills in the field. They are equipped with the necessary expertise to perform accurate and reliable inspections.
2. Compliance with industry standards: Hiring certified NDT professionals ensures that inspections are conducted in accordance with industry standards and regulations. This helps maintain quality and safety standards in various industries.
3. Quality assurance: Certified NDT professionals adhere to strict ethical standards and are committed to providing high-quality services. Their expertise and competence contribute to the overall quality assurance of products and structures.
Non-destructive testing (NDT) is a critical process in various industries, ensuring the quality, safety, and reliability of products and structures. From its early beginnings to modern applications, NDT has evolved with advancements in technology, providing more accurate and efficient inspection methods.
The different methods of NDT each have their own advantages and limitations, allowing inspectors to choose the most appropriate technique for a specific application. In industries such as aerospace and automotive, where safety and reliability are paramount, NDT plays a crucial role in ensuring the integrity of critical components. For example, ultrasonic testing is commonly used to detect internal flaws in materials, such as cracks or voids, while magnetic particle inspection is effective in identifying surface defects like cracks and discontinuities. Additionally, radiographic testing is often employed to examine the internal structure of complex assemblies, providing valuable insights into potential weaknesses. By utilizing a combination of these techniques, inspectors can thoroughly assess the quality and reliability of components, helping to prevent catastrophic failures and ensuring the overall safety of the industry.
If you’re interested in exploring more about the fascinating world of nondestructive testing (NDT), you might find this article on Wave Magnets’ website intriguing. Titled “The Role of Wave Magnets in NDT,” it delves into the significance of wave magnets in enhancing the accuracy and efficiency of NDT processes. Discover how these innovative tools can help detect flaws and defects in various materials without causing any damage. To learn more, check out the article here.
FAQs
What is NDT?
NDT stands for Non-Destructive Testing. It is a method of testing materials and components without causing damage to them.
What is an NDT book?
An NDT book is a book that provides information on Non-Destructive Testing. It may cover topics such as the different methods of NDT, the equipment used, and the applications of NDT.
Who can benefit from reading an NDT book?
Anyone who is interested in Non-Destructive Testing can benefit from reading an NDT book. This includes students, professionals, and researchers in fields such as engineering, manufacturing, and materials science.
What are some popular NDT books?
Some popular NDT books include “Introduction to Nondestructive Testing: A Training Guide” by Paul E. Mix, “Nondestructive Testing Handbook, Third Edition: Volume 1, Leak Testing” by R. Bruce Thompson, and “Nondestructive Testing Handbook, Third Edition: Volume 7, Ultrasonic Testing” by Robert C. McMaster.
Where can I buy an NDT book?
NDT books can be purchased from a variety of sources, including online retailers such as Amazon and Barnes & Noble, as well as specialty bookstores and technical publishers.
Are there any prerequisites for reading an NDT book?
Some NDT books may assume a basic understanding of engineering or materials science principles. However, many NDT books are written for a general audience and do not require any specific prerequisites. It is always a good idea to check the book’s description or reviews before purchasing to ensure it is appropriate for your level of knowledge.